Industry Partners
ISRAEL AEROSPACE INDUSTRIES (IAI) ENGINEERING DIVISION
IAI has full in-house capabilities in nearly all disciplines of aircraft development, from initial concept phase, structural and mechanical design, material science, loads, dynamics, stress, fatigue, advanced aerodynamics, heat transfer, etc. IAI also has expertise in, acoustics, CFD analysis, energy sources, structural health monitoring, NDT , automation “green” environmentally friendly materials and processes , 3D printing and other relevant technologies. Specifically, in the composite material field, IAI has over 50 years of experience in design, manufacture and certification of many parts and assemblies for CS25 size certified aircraft, as well as experience with CS23 size certification.
To compliment these capabilities IAI has a significant RESEARCH AND DEVELOPMENT TECHNOLOGY INFRASTRUCTURE INCLUDING:
- Ground testing facilities, vibration, environmental temperature, shock, fatigue
- Wind Tunnel test center
- Flight Test Center
- VR/AR Labs
- Additive Manufacturing Lab
- Ecology Lab
- Electric Propulsion Lab
- High Altitude engine testing cell
- IAI has access to certified material data bases for relevant composite material systems, both the AGATE and NCAMP programs
- Design Tools: CATIA V5, Unigraphics, PATRAN/NASTRAN
- Manufacturing capability in several composites fabrication processes: RTM, LRI, prepreg (autoclave), automation (pick-and-place, automatic fibre placement (AFP), contour tape layup
IAI has been a significant partner in the EU R&D Framework Programs. We have been a serious partner or coordinator in well over 120 EU projects, starting from the FP4 framework program in 1997
IAI is coordinating this OPTICOMS project
CORIOLIS is a specialist in the implementation of composite materials. COR develops, makes and markets robotic cells for fiber placement using a standard 6 axis robot enabling the laying of continuous or discontinuous fibers, in all directions and on complex geometrical surfaces.
COR’s objective is to develop and supply automated solutions for the manufacture of composite parts. The aim is to enhance mechanical performance thanks to low costs and an energy efficient, reliable technology that enables layup using a variety of composite materials.
Based around this expertise, the company has aggregated its robotic competences which enable it to offer exclusive equipment conceived and developed for the composites industry.
COR has filed more than twenty patents since its creation and has positioned itself today as an expert in robotic fiber placement technology.
AFP at COR:
- The fiber placement system consists of placement head, a creel and a tube for feeding the fibers. The creel provides all the necessary functions for unwinding the bobbins at high speed with low tension and enables swift ergonomic loading and unloading of the bobbins. The flexible pipes individually feed each fiber from the creel to the layup head avoiding all risks of twisting or damage to the fiber, while maintaining a low tension
- The system is compatible with pre-impregnated thermoset material certified by the aeronautic industry, but also with materials “of the future” such as dry fibers and pre-impregnated thermoplastics. This adaptation is made possible by a rapid change of the heating system. The unwinding, guiding and laying up system are already adapted to these three families of materials.
- Due to the lightness and compactness of the COR fiber placement heads, robot dynamic movements are exploited 100%, while minimising efforts, and enabling maximum productivity combined with precision control.
- The new Quantec Kuka or ABB offers improved movement combined with an increased repeatability and low consumption. These robots are perfectly adapted for placement heads of 1, 8 or 16 ¼’’ fibers.
A benchmark manufacturer of high value-added solutions in the field of grinding and turning, Danobat develops, in close collaboration with its customers, turnkey solutions for specific applications in the following sectors: aerospace, railway, automotive, energy, oil and gas. and lightning strike meshes. The Aero Consultants team offers technical consulting, hands-on support, and customer training.
Danobat contributed it’s ADMP (automated dry material placement) technology to the OPTICOMS research effort. This technology proved to be exceptionally useful due to it’s fast lay-up times, low cost material system as well as good dry material permeability , which can help ensure a successful infusion process
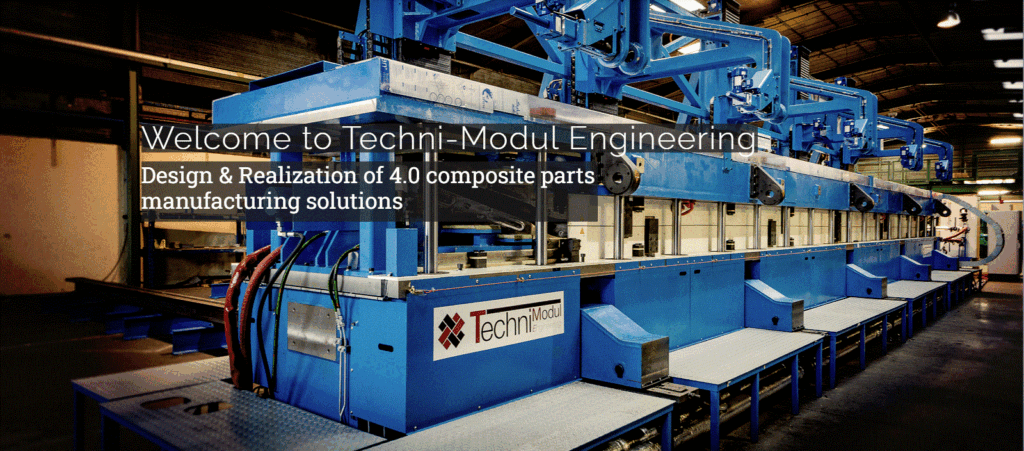
Techni-Modul Engineering (TME)
Created in December 1986, Techni-Modul Engineering (TME) is an industrial engineering company that designs, realizes and implements standardized and turn-key solutions in support of composite parts manufacturing. TME provide optimized and innovative composite manufacturing solutions worldwide for various processes and for different functions. With over 37 years of experience, TME has a proven legacy in advanced composites manufacturing solutions that enable customers to achieve high production rates at ever lower costs while always keeping quality up.
In the project OPTICOMS, TME implemented or Robotic “pick and place” composite material automated manufacturing technology to help realize the project goals.”
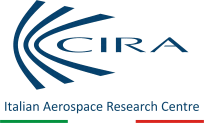
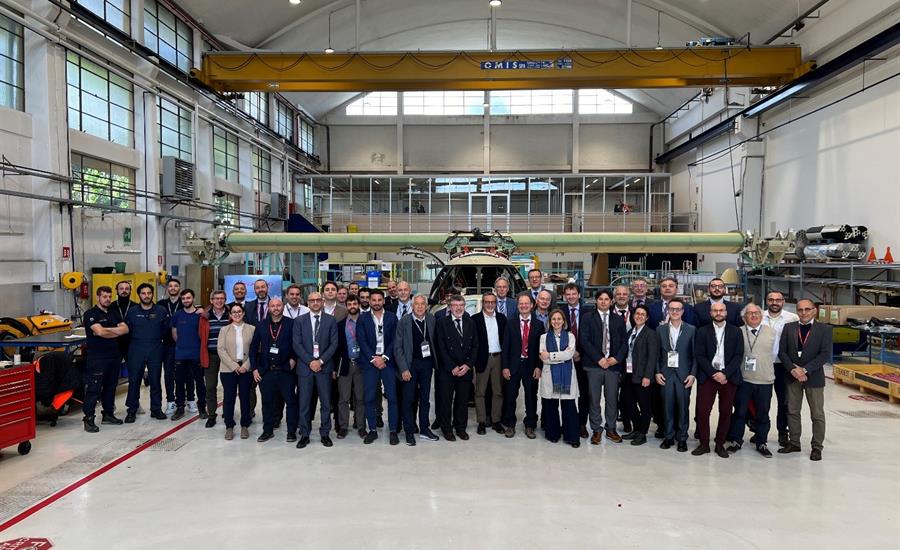
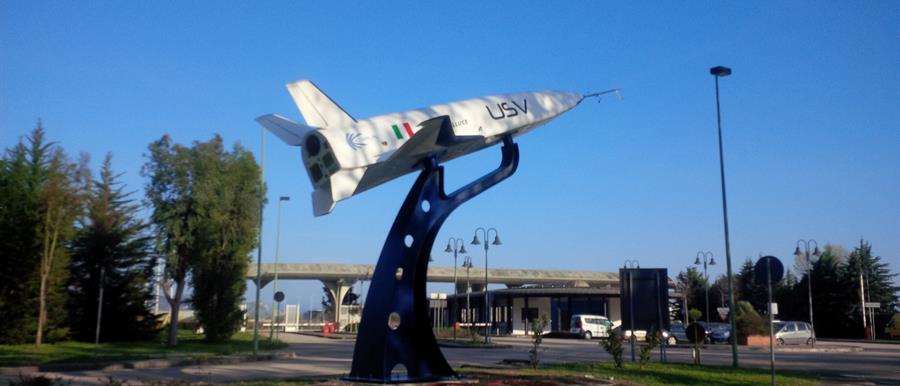