project-overview
OPTICOMS brings affordable automated composites manufacture to small aircraft category
The economic and weight-saving benefits of composite materials have been recognised for decades. However, making airplane structures in composites has proven in the past to usually be labour-intensive and challenging in terms of manufacturing affordable components of reliable quality.
Investment in automating the manufacture of large composite structural components can significantly lower the costs and improve consistency. But this luxury of large scale automation is experienced mainly by the largest airframe makers with high manufacturing volumes who have had the resources and budgets to pursue automated composite production options.
That could be about to change thanks to Clean Sky’s seven-year OPTICOMS (Optimised Composite Structures for Small Aircraft) project, which kicked off in July 2016.
Funded by the European Commission under Horizon 2020, it aims to bring innovative approaches in automated composite aircraft structure R&D to the Small Air Transport (SAT) category of aviation, enabling smaller airframe companies to justify building up automation infrastructure and realise a return on investment on low volume production.
At the project’s inception, coordinator Israel Aerospace Industries (IAI) assembled a consortium comprising three composite materials automation specialists: Coriolis, known for its Automatic Fibre Placement (AFP) technology;
Techni-Modul Engineering (TME) which uses ‘robotic pick and place’, a process that applies multiple layers of composite fabric which are then infused with a glue-like resin
and Danobat, a firm which uses a composite material automation process called ADMP (Automatic Dry Material Placement).
The project has manufactured and assembled a seven-metre long composite wing for the Piaggio Aerospace P180 in the form of an ‘integral structure.’ This means that the wing’s spars, ribs and skin are simultaneously constructed in a ‘one shot’ process, leveraging the best of the three companies’ respective technologies. The idea is to then compare, evaluate and down-select the options in line with the best results in terms of quality, cost, and speed of manufacture.
But the successful outcome of OPTICOMS depends not only on finding the best automated methods of applying and curing the multiple layers of composite materials. It’s also about the tooling side of the project. This is facilitated by three complementary projects: FITCoW and ELADINE, both coordinated by the National Institute for Aerospace Research “Elie Carafoli” (INCAS), and WIBOND, coordinated by Metitalia.
Other technologies advanced in OPTICOMS include to help reach it’s very ambitious cost and weight objectives include large scale bonding technologies, virtual testing to lower certification testing costs, out-of-autoclave material systems, working skin innovative wing design, “spring in” deformation simulation, embedded optical fibers along the bond-line to monitor the bond quality and other technologies.
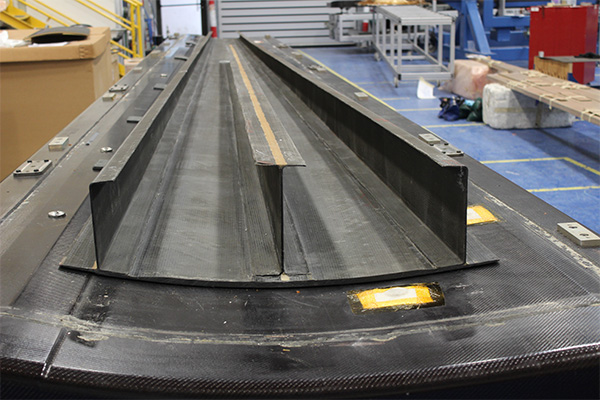
Successfully infused 7 meter integral skin-spar structure
TARGET
The project’s ambitious targets include reducing composite design and certification costs by 30%; cutting composite production costs by 40%; lowering structural weight by 20% (relative to use of metals); and trimming lifecycle costs by 20%.
Objective
The objective of the project is to develop and advance numerous technologies is order to demonstrate the economic feasibility of implementing automated composite material manufacturing for low volume production aircraft.
SOLUTION
Systematic down-selection of optimum innovative design, superior material system and most favorable automated manufacturing technology in order to achieve our ambitious goals